
Helpful Handyman Hints
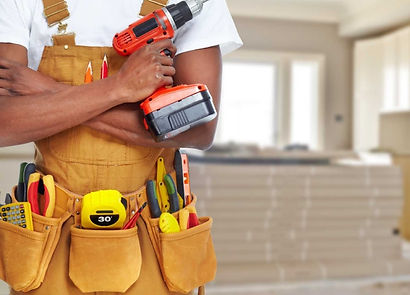

Handyman Hints: Leaving outdoor lumber unprotected is not an option
Posted by Chris Emard September 05, 2023 With 0 Comment
Some homeowners believe they have the option of staining or not staining their treated-lumber decking or fence panels.
Actually, the only options available to homeowners when it comes to real-wood decking and fencing, whether it be treated lumber or cedar, are clear coats, semi-transparent and opaque stains, or paint. Not staining or not painting isn’t so much an option as it is a choice. That’s because the decision to do nothing, or simply leave your decking lumber fend for itself, hardly qualifies as an option.
Handyman Hints: Getting the rails right
Posted by Chris Emard on April 19, 2022
So far we’ve touched on deck size, which after all things are completed, is rarely big enough.
So, know where your lot lines are and construct this backyard-living platform as large as possible. Besides, with the cost of fuel these days, walking on a deck, as opposed to walking behind a lawnmower— well, you’ll be practically making money with every step.
Handyman Hints: Facing the dreaded drip
Posted by Chris Emard on April 12, 2022
So, whoever woke up to puddle in their living room, or soaked carpet in their basement, or a decorative sunburst water stain on their kitchen ceiling a few Sundays ago, please raise their hands.
Don’t know about you, but my hand is up.
What happened? Well, if you live anywhere near the Seaway Valley, we had a regular winter going, or essentially, risk of frostbite from Monday to Wednesday. Then, really cold on Thursday. Not so cold, but still frigid enough to have to warm up the car on Friday morning.
Handyman Hints: What's on your deck?
Posted by Chris Emard on April 05, 2022
So, what are you going to finish the surface of your backyard deck with?
Most retail markets will offer three choices, with those options being treated lumber, western red cedar, and composite (PVC) planking. Sure, there are other products to choose from, such as vinyl roll-on decking, a popular choice for those homeowners who need an impermeable type of deck surface, due to their proposed platform being situated over an existing living space.
Handyman Hints: Planning for permanent shade
Posted by Chris Emard on Mar 29, 2022
So, how’s that deck plan coming along?
One week into this project should have had you minimally establishing a floor plan. If actual deck size is continuing to be a stickler in your decision-making, know this: nobody in the history of deck building has stepped back and said, “I think we went a little too big.”
Handyman Hints: Tips for getting all decked out
Posted by Chris Emard on Mar 15, 2022
So, you’re looking to build a backyard deck this spring, that’s fantastic!
Time spent in the fresh air while enjoying the peaceful serenity of reading a book, or the jovial atmosphere of friends and family— why there’s no better place to be than on a backyard deck on a warm, sunny day.
This being so, what’s the plan? How big is this deck going to be?
Handyman Hints: Hedge your purchases, or move forward?
Posted by Chris Emard on Mar 08, 2022
“We’re thinking of renovating our home this spring, but have heard there’s sometimes a six- to eight-week delay in getting windows. Is it best to put this project off?”
No, you work with your local building supply dealer, make your decision, and move forward.
“What about lumber and building materials in general? I hear the prices are moving upwards again, and, there could be delays in getting product, maybe we should delay building until next year?”
No, organize your purchases as best you can, and move forward.
Handyman Hints: A one-way conversation on hardwood flooring
Posted by Chris Emard on Mar 01, 2022
So, you’re thinking hardwood flooring for your new home build this spring, that’s fantastic.
Warm to the touch, traditional in appearance, and with every plank offering an individuality of grain artwork and natural colour variation, you can’t choose a more pleasing and satisfying floor as hardwood.
Handyman Hints: Don't neglect your garage's makeover
Posted by Chris Emard February 22, 2022 With 0 Comment
So, you’re building a home this spring, that’s terrific!
And, you’ve spent countless hours, no doubt, talking with window and door people, kitchen and bath planners, and interior designers to help you decide everything from light fixtures to what colour of socks you pull on in the morning.
However, what are your plans for the interior of the garage? You haven’t forgotten the garage, have you?
Handyman Hints: Contractors aren't mind readers
Posted by Chris Emard February 15, 2022 With 0 Comment
A fellow is walking down the beach one day, contemplating life, when he sees what appears to be a bottle sticking partway out of the sand.
As he reaches down and grasps the object, he realizes it’s not a bottle, but an Aladdin-type of oil lamp. After wiping the lamp with his beach towel, smoke emerges from the spout and a genie appears. Thankful for being freed from 100 years of confinement, the genie states he is prepared to grant the fellow 3 wishes.
Handyman Hints: Topping up your attic
Posted by Chris Emard February 8, 2022 With 0 Comment
With this whole Omicron variant thing perhaps having some homeowners a little fearful of inviting contractors into their home’s living spaces, well— how about inviting them to work in one of the non-living areas of the home, like your attic?
How do you know if your attic is in need of an insulation boost? There’ll be several clues.
Handyman Hints: Whether pink or rock wool, you can never have enough
Posted by Chris Emard February 1, 2022 With 0 Comment
Continuing with the subject of insulation, if foam board is what’s used to create a continuous insulating envelope on the outside of our homes, essentially turning our house into one big cooler, then what goes in between the 2×4 or 2×6 wood framing?
Well, that would be fibre insulation, such as Owens Corning’s pink fiberglass, or Roxul’s fiber-rock, aka mineral wool.
Handyman Hints: The right brush helps make painting easy
Posted by Chris Emard January 11, 2022 With 0 Comment
Thomas Fuller, a 17 th century British writer, once stated, “A good archer is known not by his arrows, but his aim.”
A thought-provoking quote indeed, that when scrutinized could stand for a number of sentiments. Could Leonardo da Vinci have produced the same results by having painted the Mona Lisa’with a toothbrush, as opposed to his favorite stem of crimped horsehair? Not sure.
Handyman Hints: Keep your painting fun
Posted by Chris Emard on January 4, 2022 With 0 Comment
How do we keep the task of painting, or really any type of do-it-yourself renovation project, fun? Or, at least somewhat bearable, to the point where you might actually agree to performing the task on a second occasion without too much pouting or grumbling?
Handyman Hints: Six lifelines for painting success
Posted by Chris Emard on January 18, 2022 With 0 Comment
Painting is a job, and essentially means your choice, or your spouse’s desire, to paint the inside of your home, isn’t going to be easy.
A job by any other definition still means work. However, with a few painting lifeline strategies in place, even those office softies, or persons prone to getting calluses after lifting the water cooler bottle into position and who experience difficulty working through the pain of operating a keyboard while simultaneously nursing a paper cut, well— there are tools and good practices to follow that can help guide these otherwise gifted souls to success.
Handyman Hints: The insulating qualities of foam
Posted by Chris Emard on Jan 25, 2022 With 0 Comment
Foam is regarded as a pretty good and reliable insulator.
After all, we’ve trusted those little white Styrofoam cups to keep our takeout coffee hot for years, while Styrofoam coolers have provide the best of homes for our takeout beer, safely nestling them in a bed of ice for hours.
Handyman Hints: Basement ceiling challenge-- to flatten? Or to re-route?
Posted by Chris Emard Mar 09, 2021 With 0 Comment
As we envision a living environment that doesn’t include a cracked cement floor, or walls consisting of plain concrete, partially finished drywall, and junk piled on shelves— essentially providing your basement space with the less than inspiring ‘contemporary garage sale’ style of décor, it’s important to realize the route to escaping this nightmare will run through the ceiling.
Handyman Hints: They can't read your mind
Posted by Chris Emard on January 5, 2021 With 0 Comment
You could hire the best, most experienced, most endearing, and attentive-to-detail type carpenter in the world, but if their nickname isn’t Kreskin, or if they don’t respond to “the amazing,” and if they didn’t host a mentalist TV show during the 1970s, then there’s no bloody way this well-intentioned hire is going to be able to read your mind.
Handyman Hints: Feed the hands that build for you
Posted by Chris Emard on January 12, 2021 With 0 Comment
“The way to a contractor’s heart is through their stomach.”
Well— I think that’s how the saying goes.
Regardless, every Friday, while our backyard deck renovation, which was pretty extensive, was under construction, I’d cook the fellows up some Italian sausage on the barbecue at lunch hour, as kind of a thank you for a good week’s work.
Handyman Hints: All together-- 'ceiling, trim, walls'
Posted by Chris Emard on December 22, 2020 With 0 Comment
Due to you failing to make the short list of returnees to Mrs. Sponsky’s hot-yoga class, and with there being little to watch on Netflix until HBO returns with season two of The Queen’s Gambit, escaping the doldrums of another COVID-19 winter might be best achieved by dialing in your radio to 70s rock, setting the coffee maker to its 10-cup potential, and dipping your paint brush into a can of tinted eggshell.
Posted by Chris Emard on December 17, 2019 With 0 Comment
The task of Christmas gifting doesn’t have to be such a challenge if you choose to follow one simple guideline: “make it a practical gift.”
Keep it simple, where the stress of Christmas shopping can effectively be avoided by sticking to a combination of three gift categories, them being beer, cheese, and hardware.
Posted by Chris Emard on December 26, 2019 With 0 Comment
As we look forward to four months of cold weather, short days, and general dreariness, this might be a good time to pour yourself another spiked eggnog, grab a spot on the sofa, and evaluate your home’s décor.
Posted by Chris Emard on January 1, 2020 With 0 Comment
Refurbishing a home is always a little stressful, although the cleansing process does get easier with every trip to the curb.
Ahh, the curb— the spot where a homeowner can finally lay to rest their shag area rug, macramé wall hangings, everything and anything wicker, famed artwork such as “Dogs playing cards,” and anything the colour orange, with no quarrel or judgment from neighbours, provided all is conveniently stockpiled beside a sign reading free stuff.
Posted by Chris Emard on January 7, 2020 With 0 Comment
First, some basic education. The casing is the decorative trim, or molding, that gets installed around your interior doors and windows.
Posted by Chris Emard on January 14, 2020 With 0 Comment
Today we’re installing what’s most likely the nastiest, most ornery, and to say the least, most challenging type of molding found in a home, that being the crown molding.
Posted by Chris Emard on January 21, 2020 With 0 Comment
At some point in the life of homeowners the idea of turning an existing basement, which up to this point has served the home as little more than a giant closet for junk and seasonal apparel, into real living space, will cross the kitchen table.
Posted by Chris Emard on January 28, 2020 With 0 Comment
Last week, we discussed the importance of ensuring your basement space is capable of remaining dry, essentially step one in the creation of a new living area.
Posted by Chris Emard on February 4, 2020 With 0 Comment
Sometimes, you’ve just got to get yourself out of a situation in as expedient a manner as possible.
Say you’re a teen in a home where the house rules clearly oppose the sleeping over of friends in your finished basement, with said rules especially targeting the opposite sex due to the yearnings of young love not being truly appreciated by the parental hierarchy. Then a call for breakfast wakes you both up from deep slumber; your little friend requires a quick exit.
Posted by Chris Emard on February 11, 2020 With 0 Comment
Engineered flooring shown over a basement subfloor. STEVE MAXWELL/POSTMEDIA NETWORK
If you’re finishing your basement, whether it be for it to serve as an exercise room, play area for the kids, or simply as a means of getting the TV downstairs, all in an attempt to create a more peaceful living atmosphere on the main level, you’re going to need flooring.
Posted by Chris Emard on February 18, 2020 With 0 Comment
Montreal Canadiens forward Phillip Danault (24) gets hit in the face by the puck in front of Arizona Coyotes goalie Antti Raanta (32) during the second period at the Bell Centre, on Feb. 10, 2020. ERIC BOLTE-USA TODAY SPORTS
With the subject on the table being basement floors, let’s continue with our discussion regarding basement subfloors.
Handyman Hints: Let there be light! (in your basement)
Posted by Chris Emard on Mar 16, 2021
Neanderthal: an archaic human species, possessing a robust build, averaging 60-65 inches in height, natural cave dweller, having the capacity to develop rudimentary tools for the purpose of hunting and construction.
Although thought to be extinct for at least 40,000 years, I believe the foundation and mechanical systems in our 30-year-old home were constructed and assembled by a crew of Neanderthals. Otherwise, how do you explain a basement height that averages just over seven feet, and 180 feet of concrete wall that boasts only two small windows? Fortunately, both windows are large enough to allow human access, albeit tight, but strategically undersized to prohibit entry to the raptor chasing them.
Handyman Hints: Moving onto better walls
Posted by Chris Emard on Apr 13, 2021
After semi-successfully finishing our basement ceiling — with the term “semi” relating to the fact the plumbing and mechanical ductwork were modified in order to satisfy 98 per cent of society, unfortunately leaving those individuals above 76 inches in height with the choice of either declining entry to our new basement space, or equipping themselves with protective headgear, thoughtfully provided by ourselves at the bottom of the stairs — we’re moving on to the walls.
Handyman Hints: When water ruins your perfect basement wall
Posted by Chris Emard on Apr 20, 2021
What constitutes the perfect basement wall?
Answer: one that doesn’t have a puddle of water at its base. That’s what basically defines the perfect basement wall. Puddle at the base, not good. Dry at the base, perfect.
So, regardless of how your basement wall looks, be it plain concrete or some horrible 70s style panelling, if there’s no water penetrating through to the inside, especially during those periods of spring and winter thaw, then there’s little reason to look this gifted horse in the mouth. Your perimetre concrete wall is doing its job, and is therefore, perfect.
Handyman Hints: Searching for the seep
Posted by Chris Emard on Apr 27, 2021
Pooling or water infiltration history? Consistent water entry over the last eight years, usually occurring during periods of winter thaw, spring rains, rain accompanied by winds coming from the east, uncle Jeff urinating against the home at annual family gathering, and really any moisture-related substance falling within a few feet of our east-facing foundation wall.
Handyman Hints: Floor it? Or live with it unfinished?
Posted by Chris Emard May 04, 2021
The plumbing and mechanical systems have been modified or rearranged to create a living and head-room space more receptive to those winners of the genetic lottery, at least height-wise, with ductwork related concussions and general head injuries expected to drop by at least 20 percent.
Handyman Hints: Why we dig
Posted by Chris Emard Jun 01, 2021
Just to say, if you’re going to erect a structure, and your backyard deck falls into that category, ensuring things remain level and free of movement will mean planting its feet firmly in the ground. How deep do we dig? Although prevailing rains and wind turbulence are a whole lot more severe at 100 stories high, your deck will have one foe to be wary of, and its name is frost.
Handyman Hints: Keep your deck level, consider composites
Posted by Chris Emard on Jun 22, 2021
What should be your deck’s essence?
Similar to the Seinfeld sitcom, it should be all about nothing. No curves, no separated side levels or balconies. No upper or lower levels. Build your deck as deep and as wide as possible, but most importantly, put it all on one level.
Handyman Hints: Planning your deck's 'rail' way
Posted by Chris Emard Jul 06, 2021
Although building codes can differ from municipality to municipality, deck platforms higher than two feet are going to require a spindle-and-railing system that’s at least 36 inches high. Once your deck, or balcony, rises six feet or more off the ground, you’ll require a railing system that’s at least 42 inches high.
Handyman Hints: No drawings, no permit, no rails
Posted by Chris Emard Jul 13, 2021
To review, condition one is railing height, with your railing system needing to be at least 36 or 42 inches high, depending on how high your deck is removed from the ground. Two, baluster spacing, whereby the space in between your vertical balusters shouldn’t exceed four inches. And three, post strength, whereby the newel posts will need to withstand at least 200-plus pounds of lateral pressure without deviating more than an inch or so, basically the same stress it would have to endure should the fellow batting clean-up for your men’s keg league softball team happen to lean up against it.
Handyman Hints: The first step to a good fence between good neighbours
Posted by Chris Emard Jul 20, 2021
For reasons dating back about 2,000 years, people tend to be a little sensitive when it comes to property lines. So, and because wars have been fought over boundaries, don’t just call before you dig, but just as importantly, know exactly where your property lines are before you dig.
Handyman Hints: Fencing etiquette to be a good neighbour
Posted by Chris Emard Jul 27, 2021
You don’t need a permit or licence to play golf. However, there are laws to the game that say you can’t nonchalantly kick your ball out of the rough onto a better playing surface, even if your opponent isn’t looking. And, there are rules pertaining to etiquette, with guidance provided for those individuals prone to profanity, along with suggested coping mechanisms designed to help frustrated individuals in the habit of burying the head of their putters into the green after having failed to sink what was essentially a gimmie.